Different Bus-Bar Schemes in Electrical Substations
What is a bus bar?
In Simple words, a bus-bar is a common connection point or a node for multiple incoming and outgoing circuits such as power lines or feeders.
As we know it is impractical to connect multiple conductors at one point.
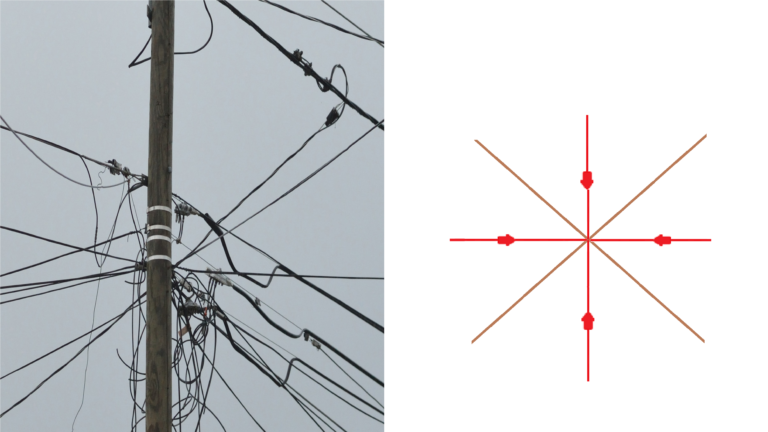
Hence we use bus bars, where these connections can be done spaciously and conveniently.
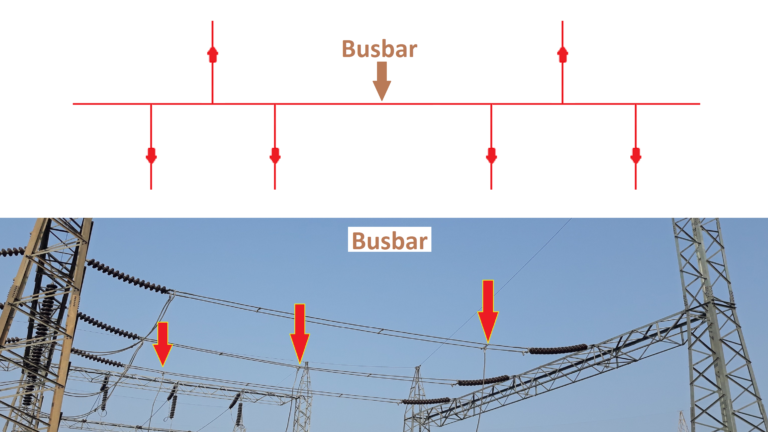
So let’s start with different bus-bar schemes or systems in an electrical substation.
1. Single Bus System
This is the most basic and simple Bus Bar system. As we can see in the diagram. In this type, all incoming and outgoing bays such as lines, transformers, and feeders are directly connected to a single bus.
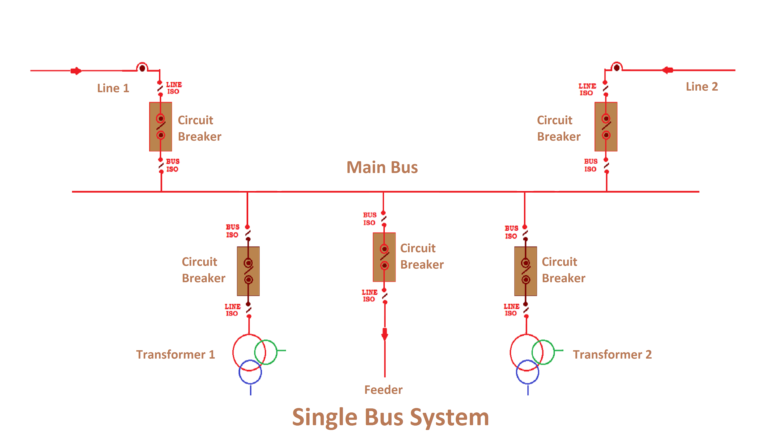
Advantages
Due to its simple design, it is easy and convenient to operate.
It is very economical, because of its least capital cost among all bus Bar systems.
Disadvantages
In this type, maintenance activity of any bay or equipment such as a transformer is not possible without service interruption of the particular bay or equipment.
In case of fault on bus or bus outage for maintenance, all the bays connected to the bus get interrupted.
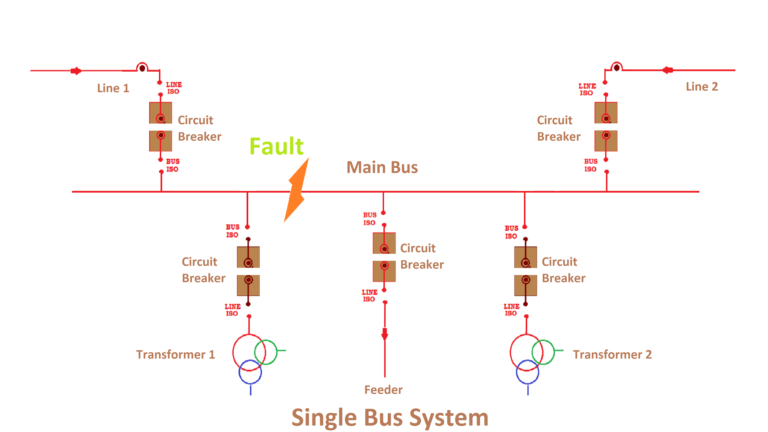
2. Single Bus with Bus Sectionalizer System
This is a single bus system, with additional circuit breaker and isolators, making two different sections of bus, hence called a single bus system with bus sectionalizer.
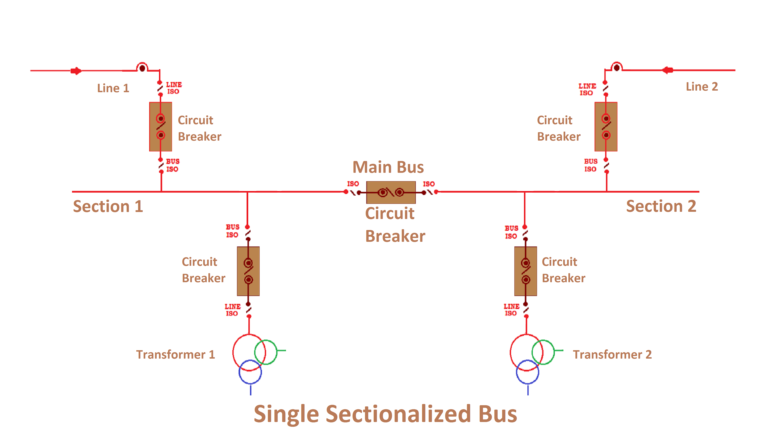
Advantages
Since there are two sections, separated by a circuit breaker, the fault on one section does not interrupt the other section of the bus. Circuit breaker isolates faulty section from the healthy one.
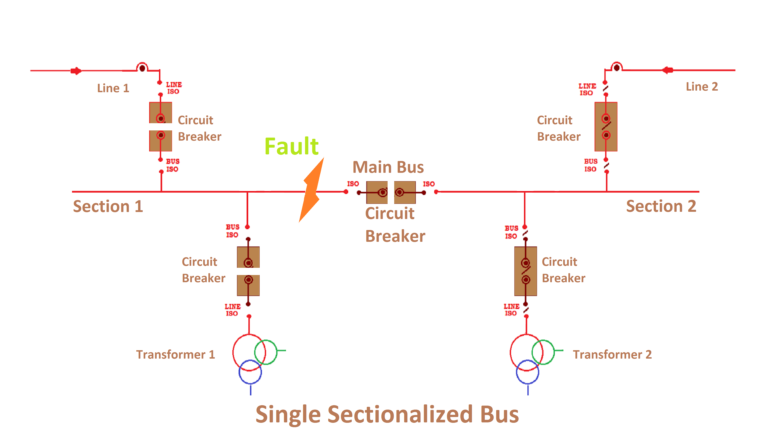
Maintenance of the bus section can be done individually, without affecting other section. Hence power supply continuity is maintained.
Disadvantages
The cost of circuit breaker and isolators is added to the capital cost.
3. Main & Transfer Bus System
As shown in the diagram. There are two buses, one main bus and the other transfer bus also called an auxiliary bus. Each bay or equipment such as line, and transformer are connected to both the buses, to main bus through circuit breaker and isolators, and to transfer bus through auxiliary isolator only. These two buses are connected by circuit breaker and isolators, called bus coupler, and this bay is called transfer bus coupler TBC bay. In normal conditions, the load of all bays is on the main bus, and the transfer bus is in standby mode, which means auxiliary isolators are open. Also, TBC bay circuit breaker and isolators are open. So this is a normal condition.
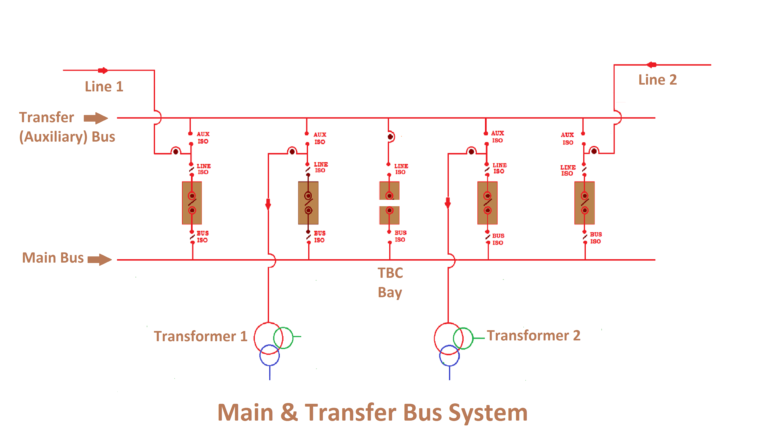
Because of such arrangements, the load of any bay can be shifted on the transfer bus. Now, for example, let’s see, how the load of transformer 1 is shifted on the transfer bus. The first auxiliary isolator of transformer 1 is closed, both isolators of TBC bay are closed, the TBC breaker is charged, the main circuit breaker of Transformer 1 is opened and then bus and line isolators of transformer 1 are opened. Hence load of transformer 1 is shifted on the transfer bus. To take the load back on the main bus exactly reverse procedure is followed. Close the bus and line isolators of transformer 1, close the circuit breaker of transformer 1, and open the TBC circuit breaker along with both TBC isolators. And then finally open the auxiliary isolator of the transformer 1.
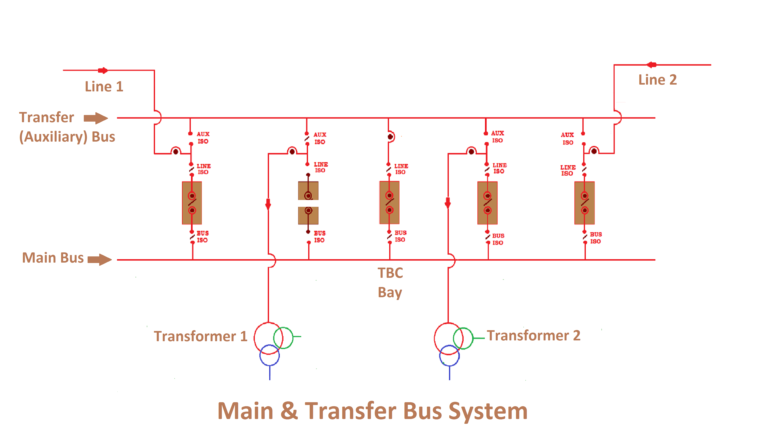
In case of fault on the main bus, all bays connected to the bus get interrupted.
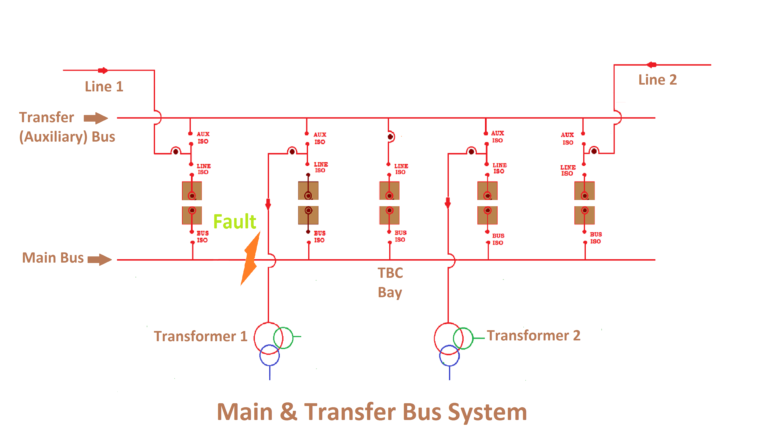
Advantages
Circuit breaker maintenance of any bay can be done without interrupting the power supply.
This arrangement provides more flexibility.
Disadvantages
The only disadvantage is that it adds up the cost of the auxiliary bus, TBC breaker, and isolators.
4. The Double Breaker Bus System
As the name says, there are two bus bars, bus 1 and bus 2, as we can see in the diagram, each bay or equipment such as a line, or a transformer is connected to both the buses, through breaker and isolators to each bus. This means each bay has two breakers for bus 1 and bus 2, hence this is called a double breaker bus system. In normal conditions, both the buses are charged.
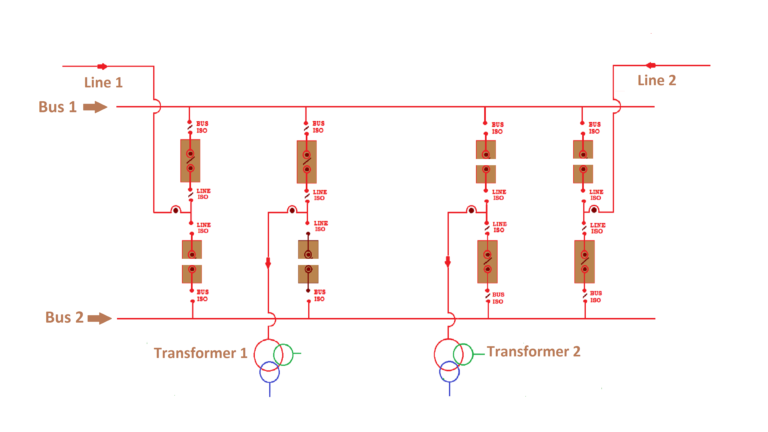
The difference between this one and the previous transfer bus system is that in this system each bay has two breakers whereas, in the case of the transfer bus system, each bay has only one breaker and auxiliary isolator. Hence this system does not require a separate TBC bay.
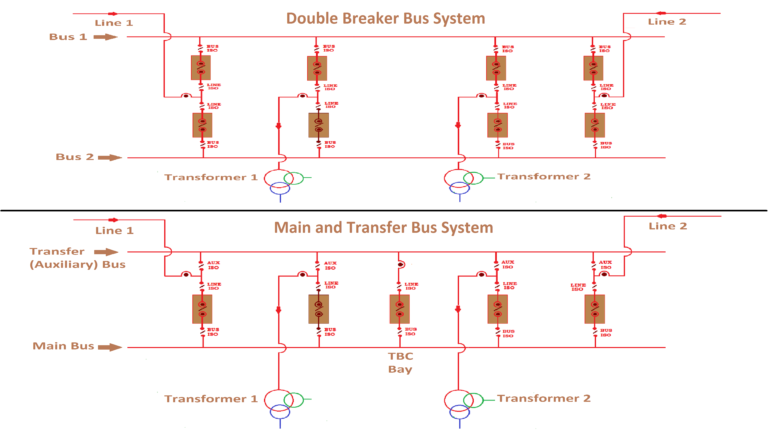
Now let’s see, how to shift load of transformer 1 from bus one to bus two. First close bus 2 side isolators, close bus 2 side circuit breaker, now open bus 1 side circuit breaker and isolators. Hence load of transformer 1 is shifted from bus 1 to bus two effortlessly. To shift load back to bus 1, the exact reverse procedure is followed. Close bus 1 side isolator and breaker, then open bus 2 side breaker and isolators.
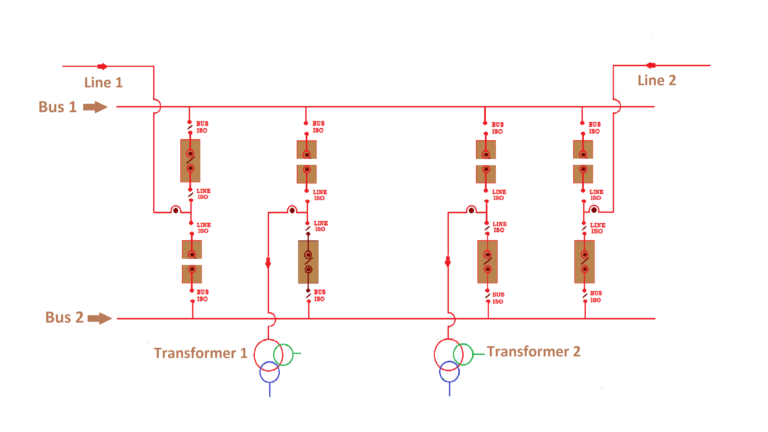
Now consider fault conditions. In case of fault on bus 1, the complete load can be shifted on bus 2.
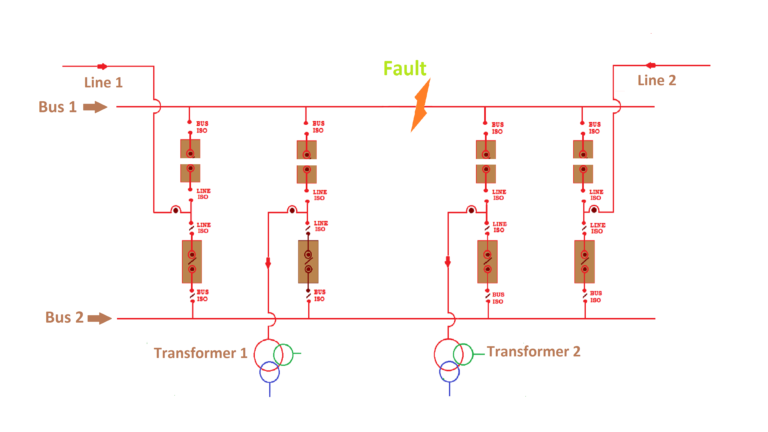
And in case of fault on bus 2, the complete load can be shifted on bus 1. Hence there is a minimal interruption in case of bus faults.
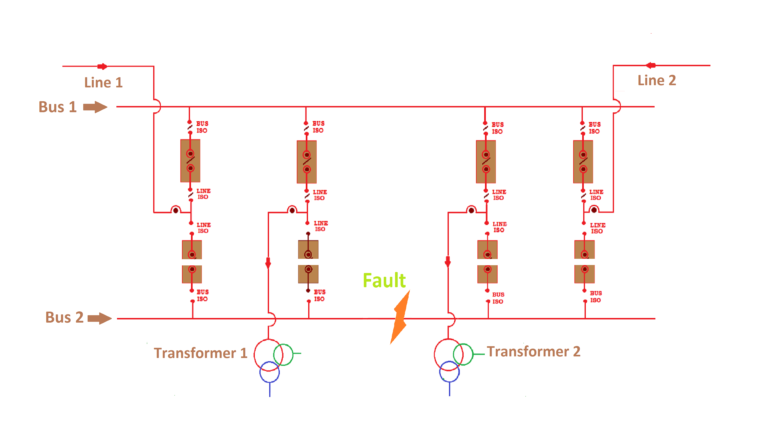
Advantages
This system is the most flexible and causes the least interruption.
Disadvantages
Capital cost is very high as two breakers are required for each bay.
5. Double Breaker Bus System with A Bus Sectionalizer
As the name says, this is nothing but a double-breaker bus system, with the addition of a bus sectionalizer to one of the buses.
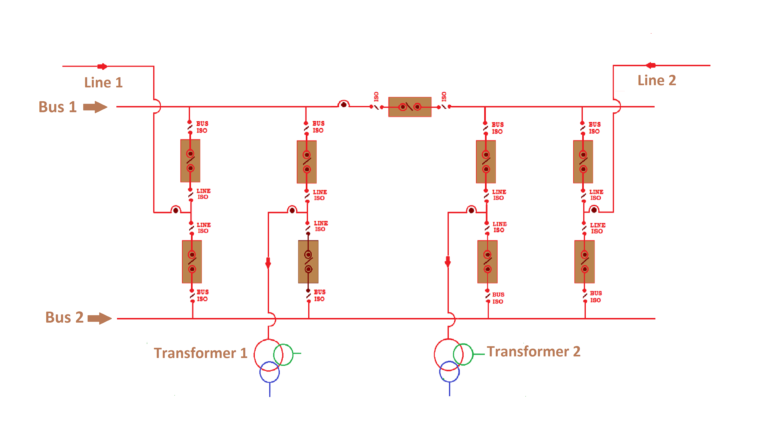
Advantages
Due to the bus sectionalizer flexibility and reliability of the system increases.
Disadvantages
This additional bus sectionalizer increases the cost and maintenance of the system.
6. One & Half Breaker Bus System
As shown in the diagram, there are two buses, bus 1 and bus 2. Respective bays are connected to bus 1 and bus 2. Line 1 and transformer 1 are connected to bus 1 through breaker and isolators. Line 2 and transformer 2 are connected to bus 2 through breaker and isolators. However, as we can see, transformer 1 and transformer 2 are connected through breaker called a tie-breaker, and isolators. Also, line 1 and line 2 are connected through tie-breaker and isolators. Hence each bay is fed through its breaker and tie-breaker, by both buses. This means both buses are charged and are in parallel through a tie-breaker. This is the normal condition.
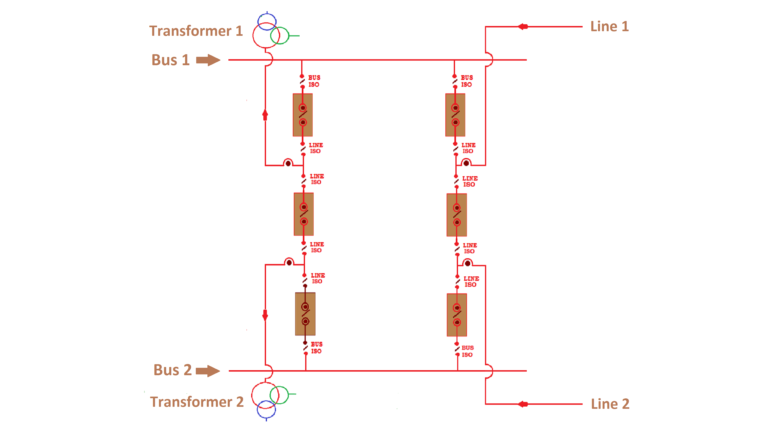
With this system, the load of any bay can be shifted on any bus, without interruption. For example, to shift load of transformer 1 and transformer 2 only on bus 1, just open the circuit breaker and isolators on bus 2 side.
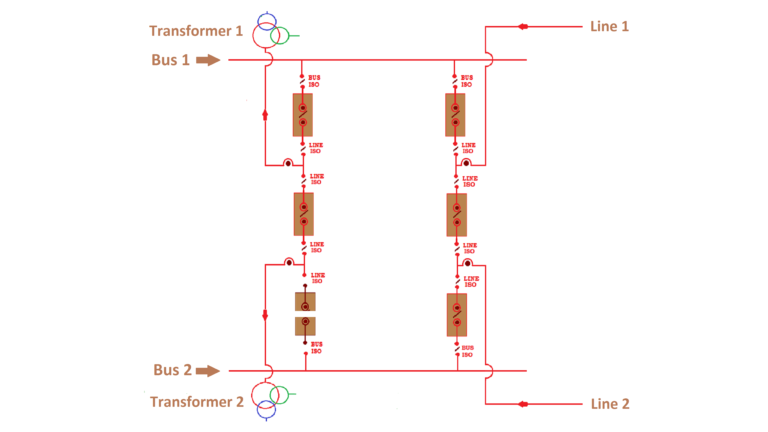
And to shift load only on bus 2 open breaker and isolators at bus 1 side.
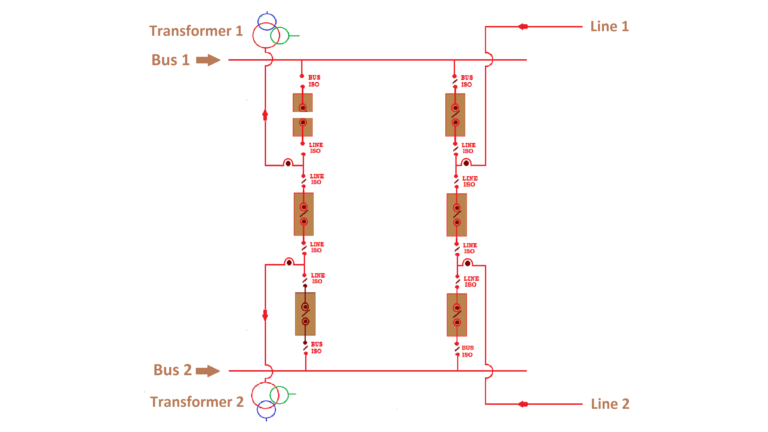
Also transformer 1 and transformer 2 can be loaded independently on bus 1 and bus 2 respectively, by opening tie-breaker and isolators. Hence maintenance of any breaker can be done without interruption.
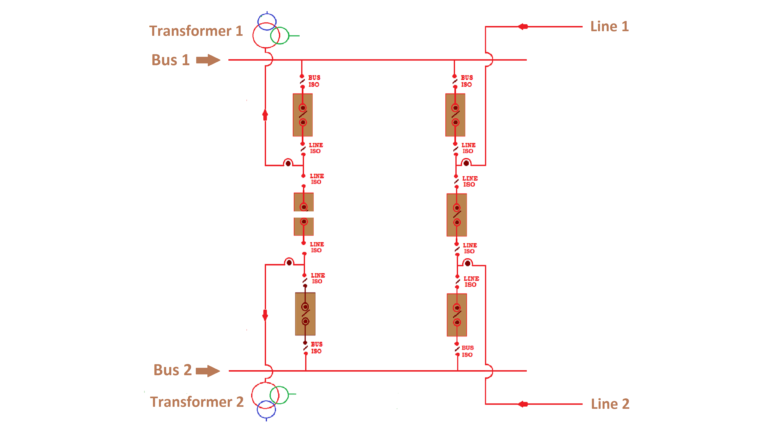
This is an improvised version of a double-breaker bus system. In the previous double breaker bus system, each bay has two breakers, which means four breakers for two bays. Whereas in this system, two bays have a common tie-breaker, which means two bays have a total of three breakers instead of four. Hence called a one and half breaker system.
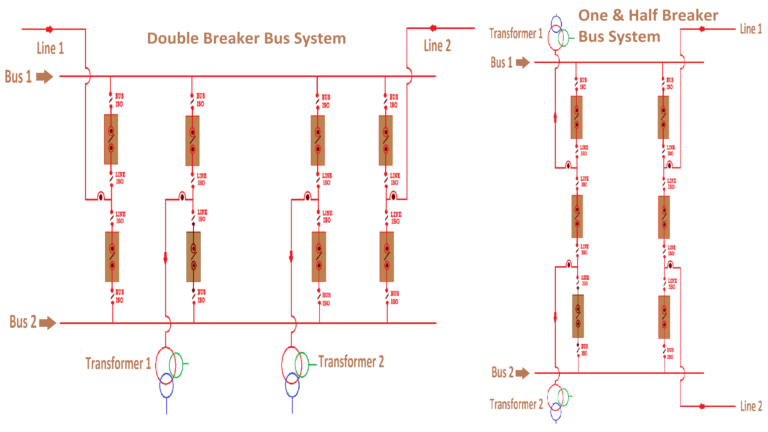
Now consider fault conditions, in case of fault on bus 1, the complete load gets shifted on bus 2.
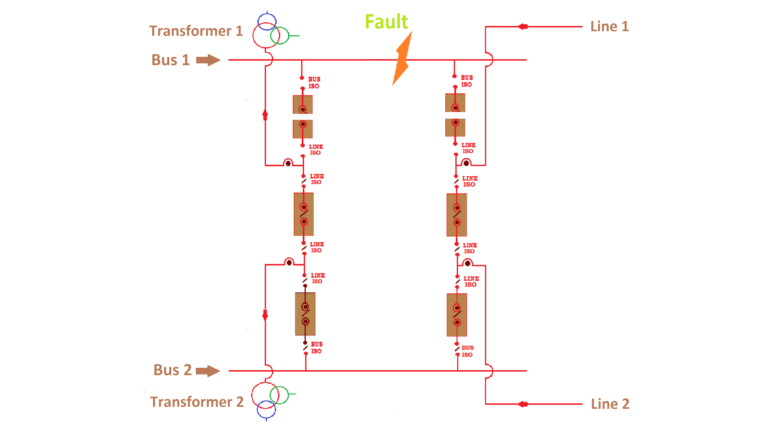
And in case of fault on bus 2, the complete load gets shifted on bus 1, without any interruption.
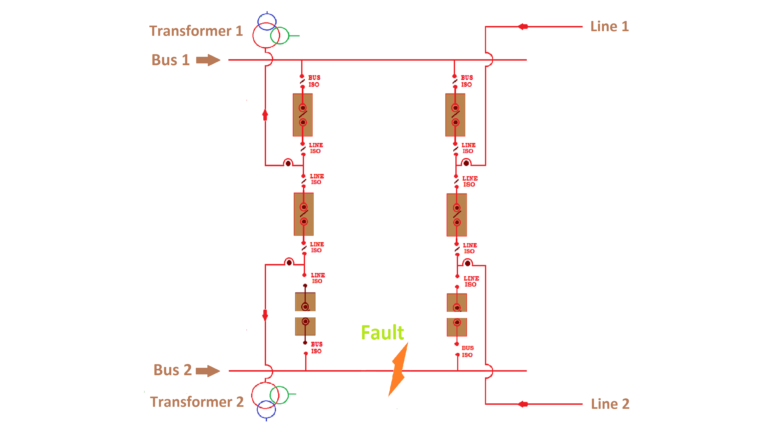
Advantages
As seen, there is no interruption at all in case of fault or failure of any one of the buses.
Disadvantages
Capital cost is high since additional tie-breaker and associated isolators are required.
7. Double Bus System with Bypass Isolators
This is nothing but a main and transfer bus system with the addition of bypass isolators to each bay. In normal conditions, we can see the load is on the main bus, with bypass isolators open.
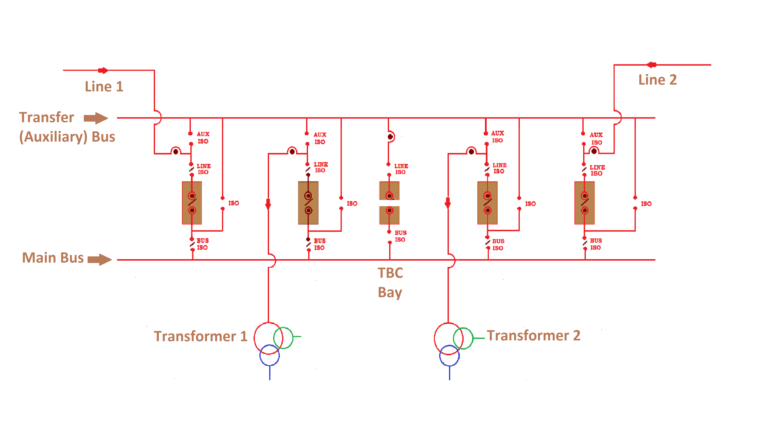
Now transfer bus can be used as the main bus, and the main bus as the transfer bus by closing bypass isolators and opening respective bus isolators. Please note that shut down is required to shift the complete load on another bus, to use as the main bus. TBC operation is the same as we discussed in the main and transfer bus system.
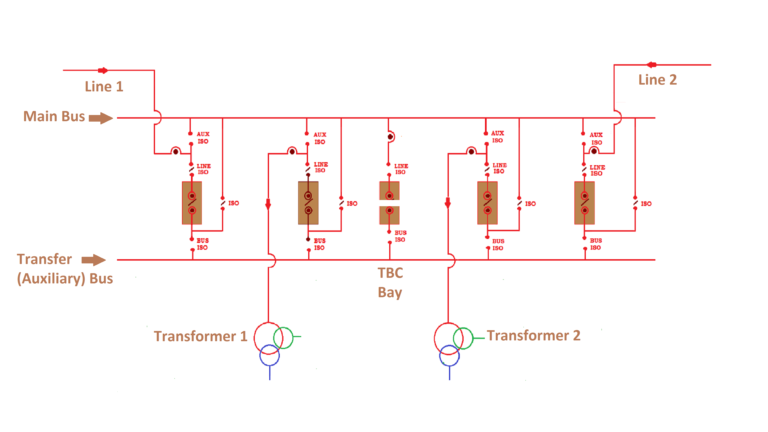
Fault on a bus interrupts complete connected load, same as in main and transfer bus system.
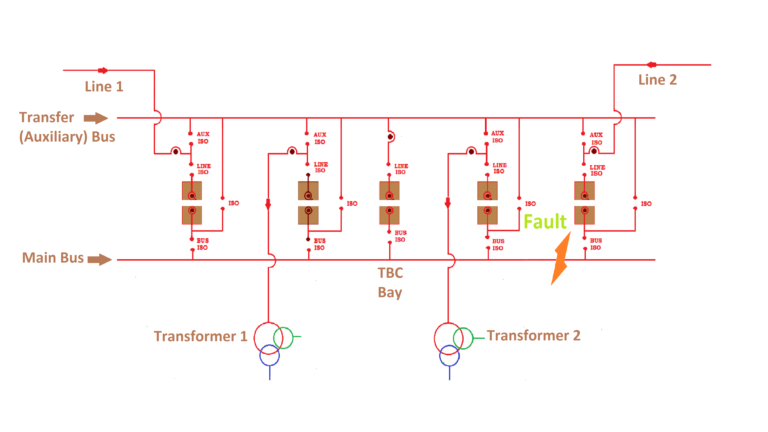
Advantages
Generally, main bus equipment is in constant service, whereas transfer bus equipment is taken in service only during maintenance of main bus equipment. But due to this arrangement, the role of the main and transfer bus can be interchanged, and we can use the equipment alternatively. This increases the lifespan of all the equipment altogether.
Disadvantages
The cost of the bypass isolator is added to the capital cost.
8. Ring Main Bus System
This is an improvised version of sectionalized bus bar system. As shown in the diagram, sectionalized bus bar ends are connected with another bus bar, with bus couplers to form a closed loop. Hence called as ring main bus system. And on the loop different incoming and outgoing circuits are connected, such as line 1 with its breaker and isolators, similarly line 2, transformer 1, transformer 2, feeder 1 & feeder 2 with their respective breakers and isolators.
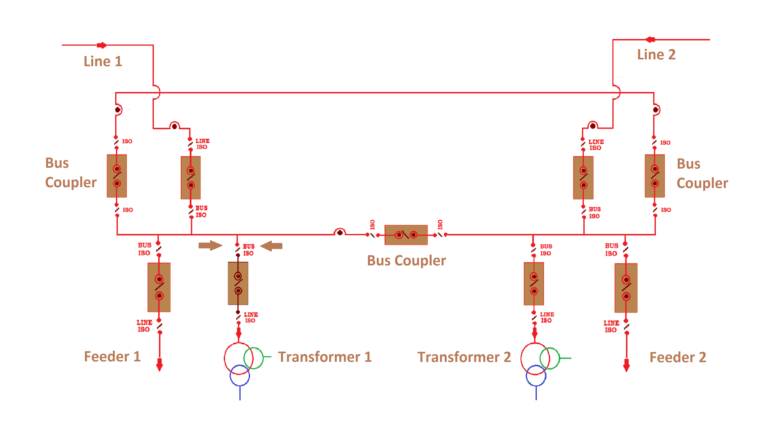
Advantages
In this system double feed is provided to each bay. In case of failure of any one of the feeds, other feeds continue to supply the feeder, hence no interruption. So maintenance of any breaker can be done without any interruption.
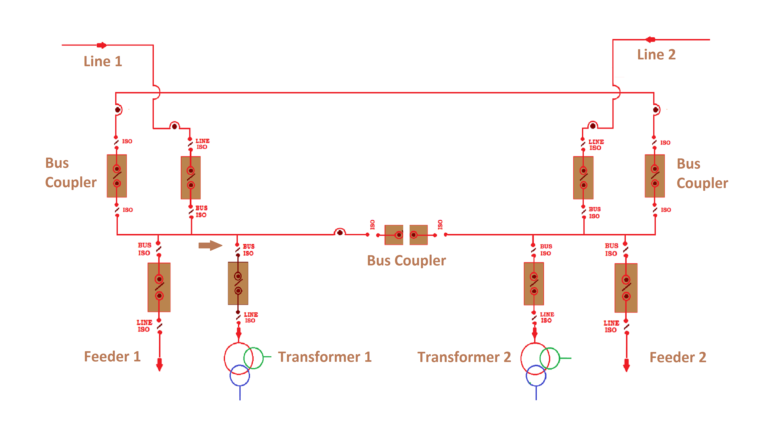
Also in case of fault on a bus, only associated breakers get tripped, hence fault does not interrupt complete load. Thus fault is localized.
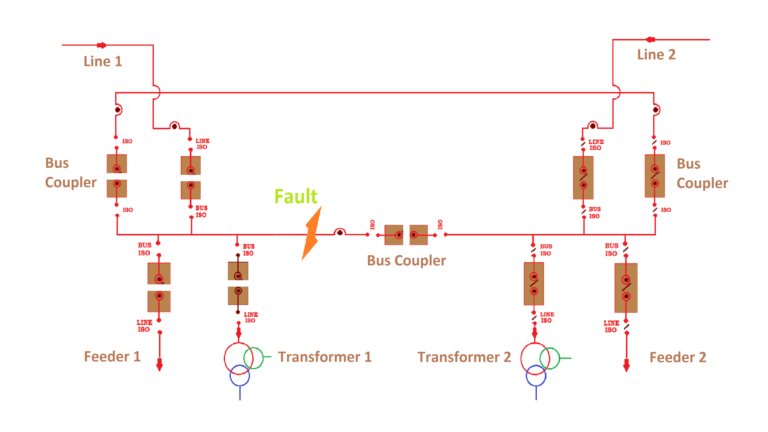
Disadvantages
If any one of the breakers is under outage, which makes it open. During this time, if any other breaker trips, it may affect one or more than one bays, depending upon the location of a tripped breaker.
Also, the load may imbalance in case any one of the breakers is opened.
9. Mesh Bus System
As shown in the diagram, in this type breakers are connected with the mesh formation of the bus. As we can see, bays are connected to node points of mesh. Here line 1, line 2, transformer 1, transformer 2, feeder 1, 2, 3 & 4 are connected to node points. That means eight bays are controlled by four circuit breakers. This system is used in the substation with a large number of circuits.
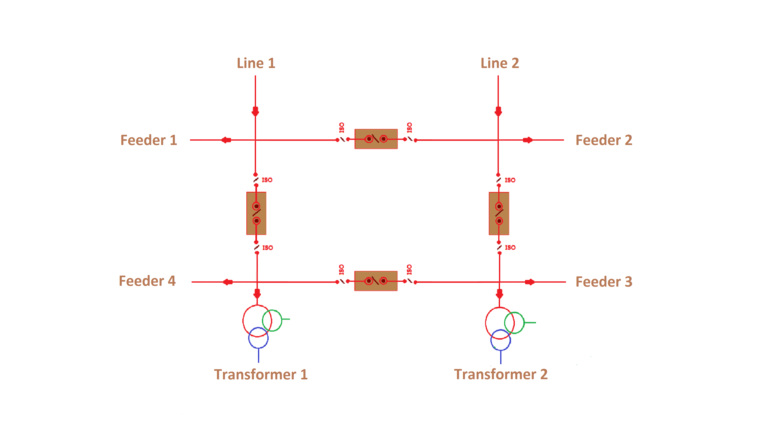
Advantages
In case of fault on a bus, both side circuit breakers open. And the fault is localized. Hence complete load is not affected.
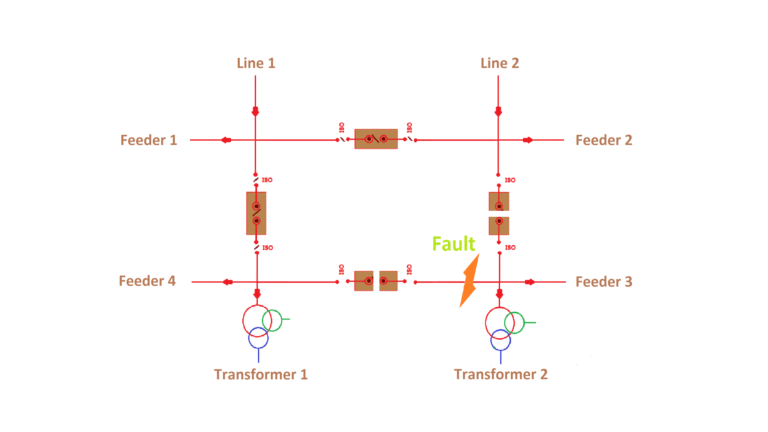
Disadvantages
This type of system provides a limited switching facility since two circuit breakers jointly control two circuits at node points.
Following important points are taken into account, to select a suitable bus-bar systems.
Cost-effective. Bus-bar scheme considered for any particular substation should deliver all the requirements with minimal capital cost.
Should have Simple and easy maintenance.
Should be easy to take outages, without or minimal supply interruptions.
Bus bar schemes should be suitable for any upcoming future modifications at that particular substation.